【PR】この記事には広告を含む場合があります。
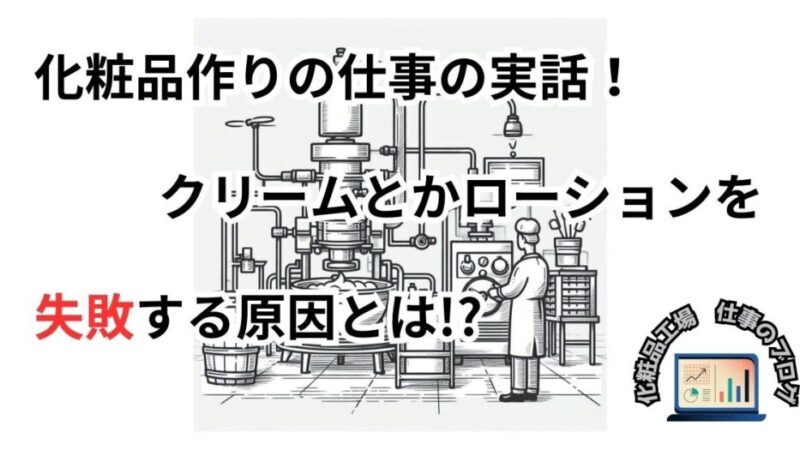
どんなに熟練した職人でも、ミスを起こすことはあります。
しかし、ミスというのは何よりも自分の信頼性を失う原因となる行為です。
これから化粧品の中身を作る「バルク製造」で働きたいと考えている。もしくは、新人として既に「バルク製造」で働き出している。そのような方に伝えたい内容です。
この記事では実際に新人が陥りやすい、バルク製造ミスを5つ紹介いたします。だれもが「やらかしてしまう」ミスといってもいいでしょう。
そして、そのミスの発生原因は、新人ならではの「気持ちの問題」が大きくかかわっています。
成長していく過程として、「ミス」を避けては通れません。しかし、事前によくあるミスを知ることで、その「ミス」は最小限に抑えることはできます。

自己紹介させて頂きます。コテツと申します。
化粧品工場での25年以上の勤務経験があり、その中でも中小規模の工場での豊富な経験を持っています。工場長としても活躍し、この業界の魅力や仕事の流れを、多く学び取ってきました。
化粧品工場で働くことは難しいことではありません。テレビCMで名を聞く大手企業の工場はごく一部であり、日本に存在する多くは中小規模の化粧品工場です。
あなたが未経験者であっても、活躍する機会がたくさんあることをお伝えしていきます。
さぁ、スタートしましょう!!
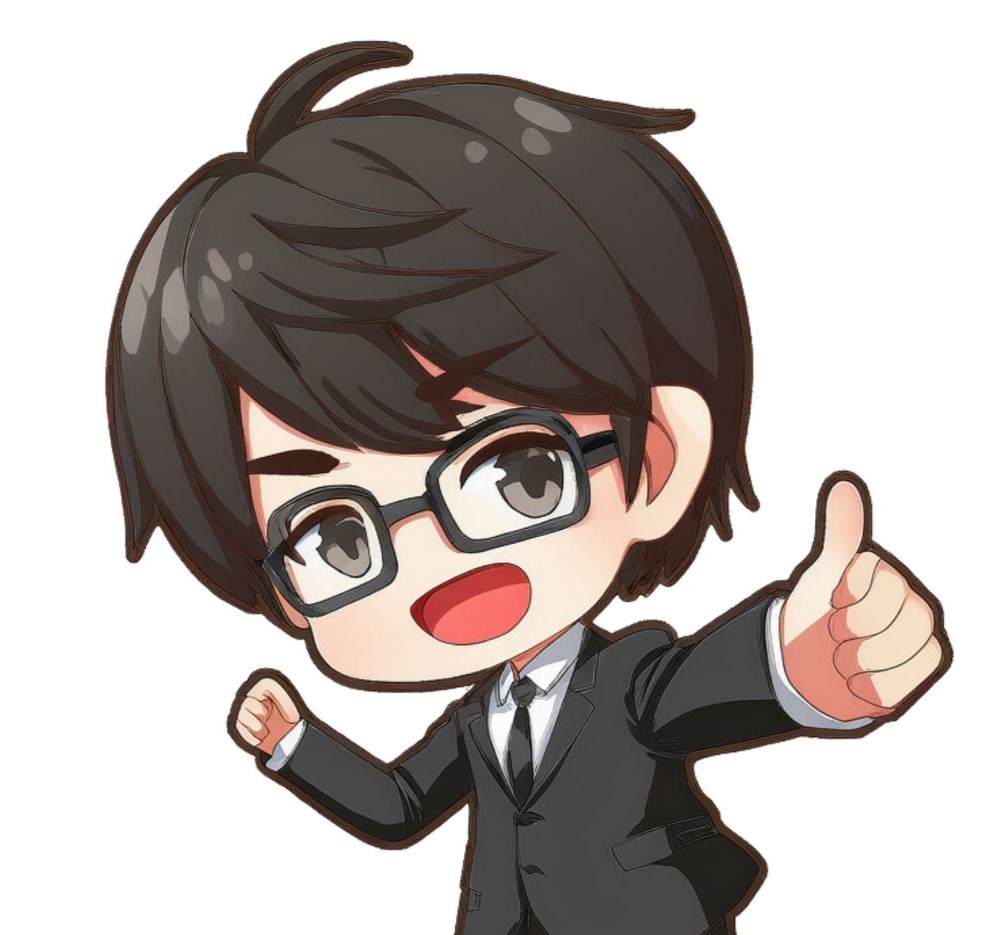
よろしくお願いします。
化粧品工場のバルク製造とは
化粧品工場で化粧品の中身を作る仕事を「バルク製造」と言います。
ですから、クリームやローションなどの化粧品の中身を作る担当部門も「バルク製造」となります。
しかし、工場によって呼び名が異なる事も多いです。「バルク調合」もしくは「製造」などと呼ばれています。
「バルク製造」がどのような仕事であるか、youtubeを引用させていただいたので、バルク製造も含めた化粧品工場の環境や仕事風景をご確認ください。
https://www.youtube.com/watch?v=f01WE-KSnJc
⇧参考動画、ミックコスモチャンネル/【大人の社会見学】たった60秒で分かる!化粧品ができるまで!
焦りが招く作業ミスの原因
新人が装置を使い「バルク製造」を任された場合、「ミス」の多くは、「うっかりミス」や「ポカミス」ではありません。
集中はしていますが、経験が浅いので「緊張」もしています。
そして「緊張状態」で考えることは「無事に早く終わらせたい」なのです。
この「終わらせたい」という焦る気持ちが、作業中の「異変」を見逃し、結果として作業ミスに繋がります。
ミスの発生となる、新人の心理
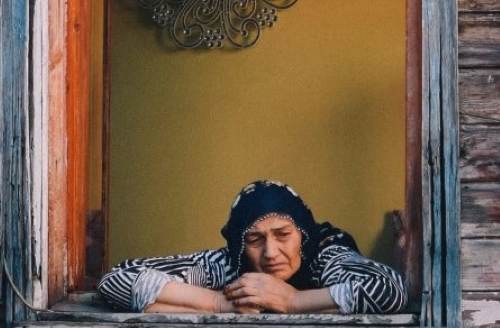
新人などの経験が浅いからこそ起きるミスを紹介します。
先ほど説明した「早く終わらせたい」の心理が、影響するものが多いです。
発生ミス、その1 化粧品を作る工程で起きる「泡噛み」とは?
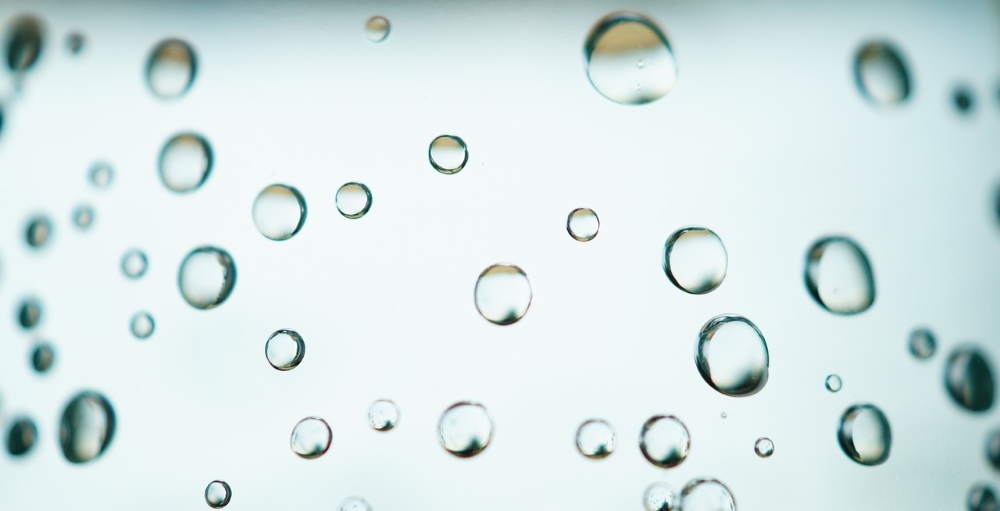
先ほどの動画でも使用されていた「バルク製造」の装置が「真空乳化装置」です。
装置の内容も含め「バルク製造」の仕事内容について解説している記事です。ご参照ください⇩
「真空乳化装置」の「真空」とは化粧品の中身を作るときに、装置内の空気を抜くことができます。
基本的に「クリーム」でも「ローション」でも空気に触れると「酸化」が進みます。ですから空気を含まないように作るのです。
逆に空気を含んだ状態とはどのような状態かというと、クリームやジェルの中に「気泡」が多く含まれています。
それを「泡噛み」と読んでいます。
泡噛みが起きる原因とは
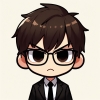
噛んだ泡は抜けないの?
「粘性がない」すなわち、滑らかでサラっとした水のようなローションの場合、泡が混ざっても直ちに抜けてしまうため、問題ありません。
しかし、もっと粘り気の強いクリームやジェルなどは、一度泡が混ざると、それが自然に消えるまで、相当な時間が必要となります。
こういった泡が混ざった状態、「泡噛み」のままでは、品質が保証できないのでお客様にはお渡しできません。このような状態は「不合格」の判定になります。
新入などは特に、化粧品を作る過程で、原料を混ぜ合わせる「混合」作業を行う際、化粧品の中身の状態を十分に確認せずに、指示通りの時間や速度だけを重視する傾向があります。
化粧品の製造量は、受けた注文数によって変わります。そして、工場によりますが、同じ製品でも作る量が毎回違うことは珍しくありません。
例えば、いつもより作る量が少ない場合では、いつもと同じ混合時間やスピードであると、「泡噛み」が発生する可能性があります。
そして、化粧品を作る基本的な工程、いわゆる「バルク製造」は以下のようになります。
- 原料を投入して混ぜる
- 混ぜながら加熱する
- さらに混ぜながら冷却する
高温では粘性も低くなるので、「真空乳化装置」という機械を使って空気を抜く「脱泡」作業で泡を解消することができます。しかし、工程を終えて冷たくなり固まった状態で「脱泡」を試みると、非常に難しい作業となります。
もし「脱泡」ができなければ、それは作業の手順にミスがあった「工程ミス」を意味します。そして、その化粧品は「不合格」となります。
「手直し」として、泡を取り除くための「脱泡作業」を行えば、「合格」にすることはできます。
しかし、この「脱泡作業」の手間と時間は、元の製造時間とあまり変わらないのです。
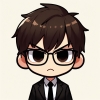
例え「手直し」できたとしてもタダでは済まないわけです。
手直し作業時間×人件費=会社の損失。ですからね。
どうして泡噛みになってしまうのか
問題が生じた時、新人がよく陥る心理状態があります。
それは、「焦り」と「楽観」の両方から「このままでも大丈夫」と思い込んで、一度始めた作業を中断しないことです。
でも、それは大きな誤りです。
- ちょっとした異変でも作業を止める。
- 小さなことでも通常と違うと感じたら、上長に報告。
ここは確実に実行しましょう。
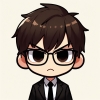
マニュアル通り進行してもミスは起きるの?
マニュアルはあります。しかし、作業がマニュアル通りに進んでも、ミスが発生することがあるという事を理解する必要があります。
例えば、化粧品を製造する工場では、注文数が常に一定ではありません。前回5000本のクリームを作ったとしても、次の注文では3000本に減ることがあります。そして、製品を作る量が違うと、それは製造の時間や手順に影響を与えます。
また、料理を作るのと同じように、化粧品を作るための原材料はいつでも同じ品質ではないかもしれません。このことから、「マニュアル通りに作業を行う」にも一定の柔軟性が求められます。
例えば、工程の一部として「加熱溶解時間」や「混合スピード」が指定されているとします。
加熱溶解後
混合時間 10~20分
回転スピード 20~35rpm
仕込み量などを考慮して調整
しかし、これらの指示はあくまでも目安であり、実際の作業では、作る量やその時の状態により時間やスピードを目で見て調整する必要があります。
さらに、工場の設備によっては、季節にて「加熱」や「冷却」のスピードが変わることもあります。
このような理由から、全てを数値化し、マニュアル通りに行うのは難しい場面もあります。
それでも、いつもの違うと感じたのなら、その都度、作業を止め、上長に報告すること。そして、マニュアルに対する柔軟な対応を持つこと。
これらを忘れずに、作業を進めてください。
泡噛みを起こさない為には
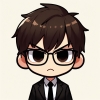
マニュアルはあるけど、職人的な要素も必要だね。
設定されたものだけではなく、原料の溶け具合などの混合状態を、装置の中を覗き判断することが多い仕事です。
だからこそ新人であれば迷うことも多く、ミスも出ます。
しかし、経験を活かすためにも、状態をよく確認して異変があれば報告。そして、正しい対応をすることで、問題なく工程を終わらせることができます。
使用する原料や作るものによって「泡噛み」しやすいモノはあります。
新商品であれば、実際に作ってみないと、どこまで対応できるかを見抜くのは難しいです。
だからこそ、「泡が多い」と思ったら、勇気をもって装置を止めましょう。
発生ミス、その2 「添加スピード」が速すぎる
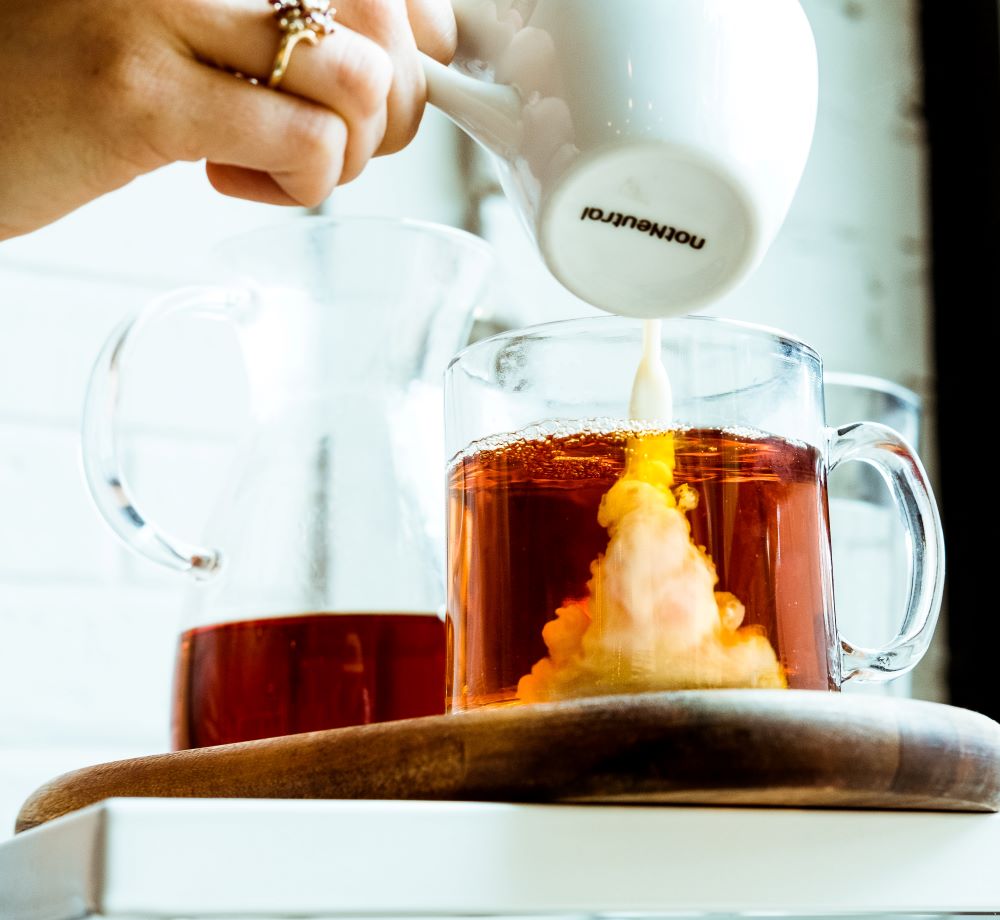
「乳化」を御存じでしょうか、「水」と「油」が混ざり白く濁る状態が「乳化」です。
クリームを作るのであれば「乳化」となります。
作り方は色々ありますが、装置の中に「油」を高温で溶解しておく、そこに高温にした「水」を加えて作る方法が1番多いかと思います。
添加スピードがなぜ影響するのか
先ほどの、クリームを作る基本は「油」に「水」の添加です。
作り方も使用する原料も色々とありますが、「油」と「界面活性剤」、そこに「水」を徐々に加えて作ります。
新人であると、「水」の添加が、どうしても早くなりがちです。
固めのクリームなどは、添加する「水」を少しずつ入れないと、一気に固いクリーム状になり、添加途中の「水」が混ざらなくなります。
少しずつ添加して、少しずつ「クリーム状」にすることで、一気に固くならず最後まで「水」が混ざるのです。
しかし、「クリーム状にならない」ことを心配しすぎて、状態確認を焦って早く添加します。そして添加途中で固くなったとしても、なぜかスピードを落とさず添加し続けます。
これも、添加した「水」が混ざらないなら、すぐに添加を止めればいいのですが、「新人の心理」が働き、「水」が混ざらなくても、結果を急いで添加を続けるわけです。
装置の中は完全に「クリーム」と「水」の二層状態です。
これを手直しするには、棒を突っ込んで手動で混合することが多く腕がパンパンになります。
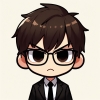
水の添加の時間を決めればいいんじゃない。
ある程度の時間は決まっています。例えば「添加時間の目安として10分」のようにです。
ただし、「水」を添加しているときの「量」はわかりません。「1分で1リットル」などと計っているわけではないので、「目分量」です。
これを「新人の心理」で焦って5分で入れてしまうわけです。
「早く入れてしまうぐらいなら、少し遅い方がいい」伝えても5分で入れたりします。
添加スピードを正しくするには
この場合は上長に相談し、添加している間は一緒に確認してもらいましょう。
正しい添加時間を知ることもそうですが、上長が確認することで「責任」も上長に移ります。「責任」という重い荷物を下ろすことで、冷静に工程を見直すことができます。
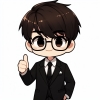
「忙しいかも」などと遠慮しないで、上長に声をかけましょう。
失敗したら元も子もないですから。
ちなみに、この添加スビートの問題は、例えとして「クリーム」としましたが、多くの品種で重要な内容となります。
モノによっては化学反応で反応熱が起きます。一気に添加したら沸騰して装置から吹き出ることもあります。
危険性がある仕事を新人に任せることはないですが、添加スピードに指示がある工程は、添加する全体量と添加時間から、1分で使用する量の容積に目安を付けてから添加しましょう。
時間配分を意識していけば、徐々にうまく出来るようになります。
うまくなるほどに、おもしろくなり、作業する「焦り」も薄れていくでしょう。
化粧品の中身を作る「バルク製造がおもしろい」を説明した内容となります。ご参照ください⇩
発生ミス、その3 装置内で起きる「焼け」とは
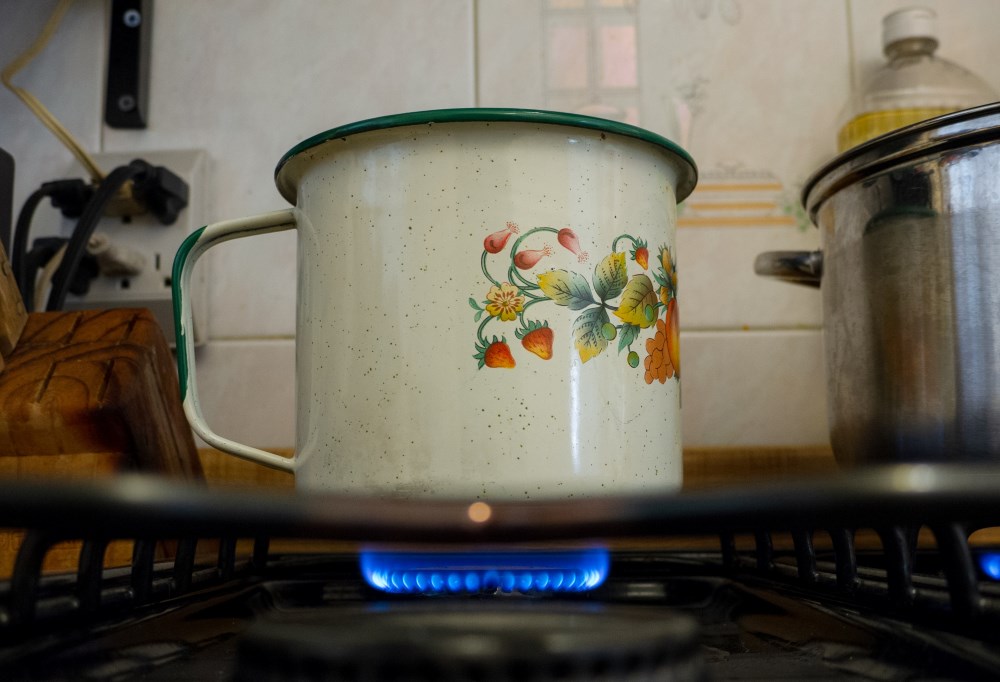
化粧品を作る「バルク製造」とは原料を装置に投入して混合しながら加熱をします。
使用する原料などで「焼け」という現象を起こすことがあります。
焼け、とは原料が高温で焼ける
クリームなどは、原料を加熱し混合して「冷却」することで、クリーム状の固さになります。
しかし、扱う製品によっては、加熱している状態から、粘性が上がり固さが出てしまうものも存在します。
「粘性がある」ものに加熱を続けると「焼け」が起きることがあるのです。
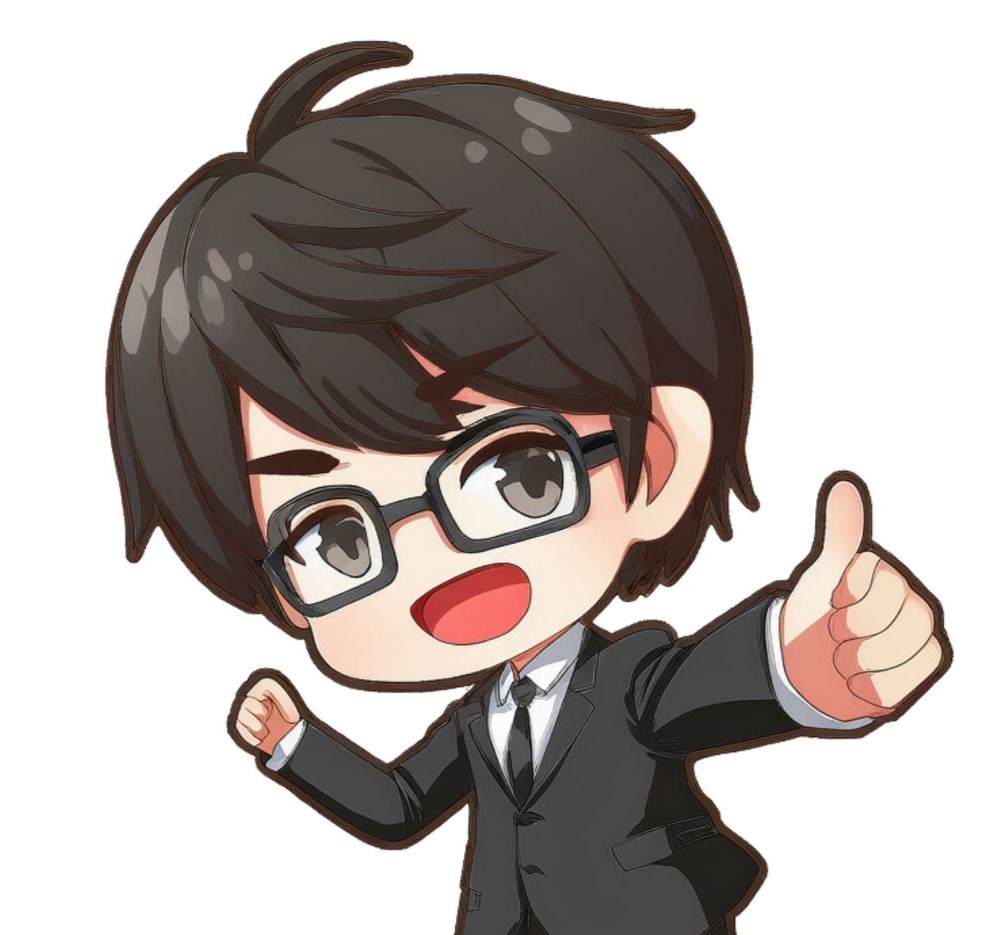
カレーを作って、コトコトと煮ているときの火加減が強いと焦げてしまうのと同じだね。
カレーも店で提供するなら、焦げたものは出せないでしょう。
化粧品も同じであり、「焼け」によって固くなったダマのようなものが発生すると、製品として不合格となります。
焼け、が発生する原因
「粘性がある」ものほど加熱によって「焼け」が起きやすいです。そして、その工程に対する指示はあります。
しかし。粘性があがっていく状態はいつも同じとは限りません。「作る量」「熱の伝わり方」「混合のスピード」など、固くなっていく状態にも色々とあります。
溶解時間、10~15分。状態を確認して時間調整。
このような指示があっても、新人からすれば「状態確認」といわれても、よくわかりません。
とりあえず溶け残りがないように、しっかり15分、加熱し溶解しておこう。思うのです。
装置の中でグツグツと煮えていたとしても、そのままです。一旦加熱を止めるなどもなく、不安な気持ちを抑えながら、そのまま時間の経過を待ちます。
原料は溶けたでしょうが、「焼け」てしまった可能性は高いです。
焼け、を起こさない為には
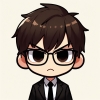
そんなに難しいなら、最初は指導者がついて教えるべきでしょ。
最初は指導者が付き、説明を受けます。その時は理解するのですが、1人で任された途端に不安な心理状態から、工程を焦って進めたりします。
「焼け」の現象はわかりにくいことも多いです。ましてや工程を焦って「早く終わらせたい」気持ちであれば、なおさらです。
覚えてほしいのは、「焼け」の現象は、加熱でおきます。粘性のある固い状態で部分的に熱が強く当たっていると思ったら、加熱を止めて上長に報告です。
そして「焼け」が起こりやすい原料はある程度決まっています。どの原料が「焼け」が起きやすいか意識することも重要です。
装置内の淵で、作っている化粧品がグツグツと沸騰するようであれば、加熱は止めて上長へ報告です。
止める時は絶対に「混合」は止めてはいけません。混ざっていないと「焼け」てしまいます。
発生ミス、その4 温度調整、「オーバーシュート」とは
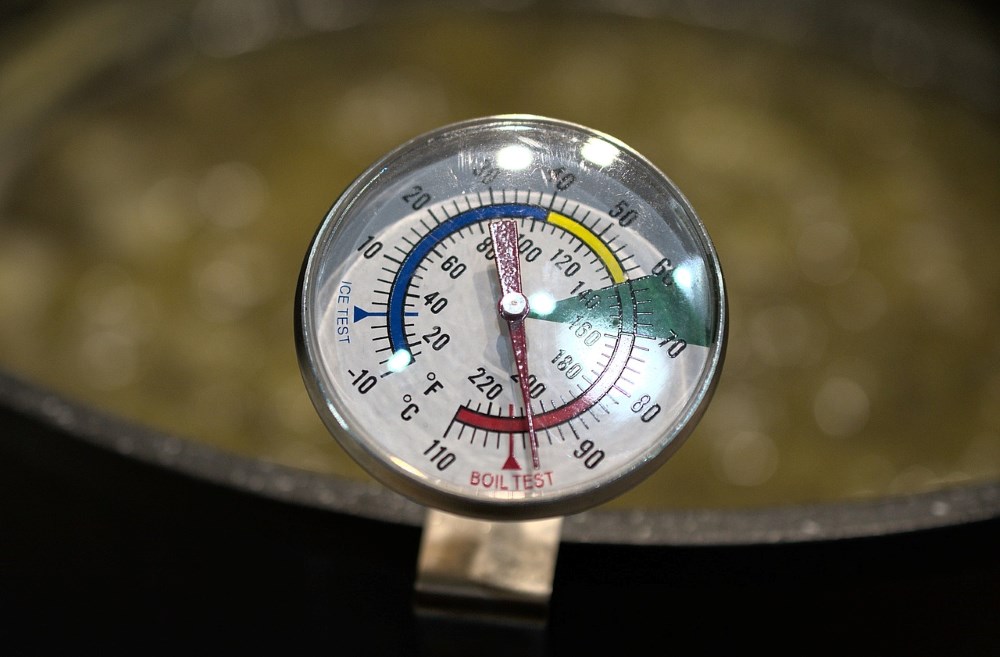
化粧品工場の「バルク製造」において、温度の調整は非常に重要となります。
化粧品を作る工程にて
- 加熱80℃10分混合
- 冷却40℃香料添加混合
などの温度による工程指示は多くあります。
機械で設定し、その温度に到達すれば、次の工程に従えばよいわけです。
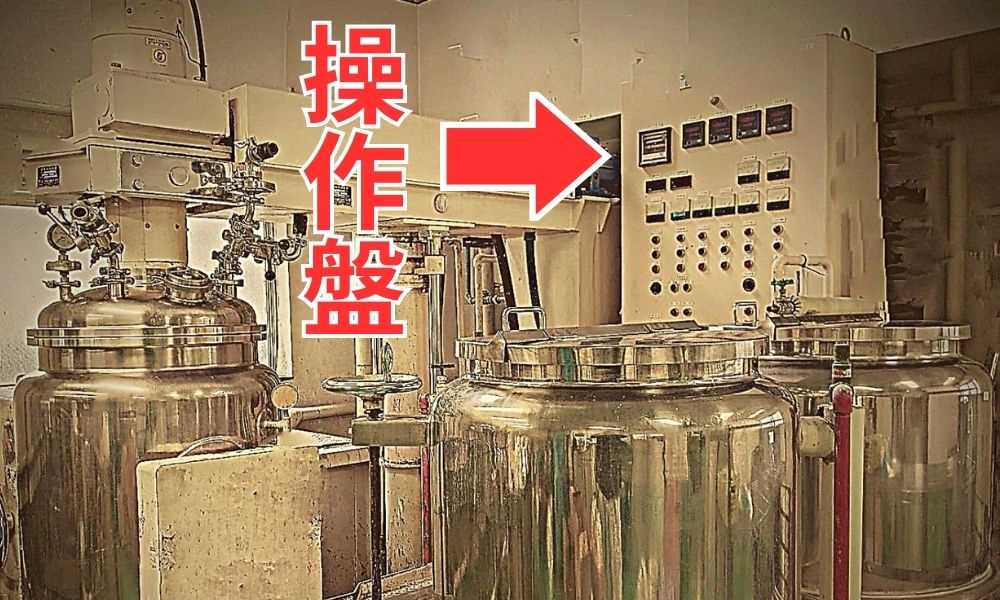
※写真の説明: 真空乳化装置の「操作盤」から温度が設定ができます。
しかし、設定しても「温度」はピタッと止まることはありません。
加熱温度を80℃に設定したのに90℃まで上昇したり、冷却温度を40度に設定したのに30℃まで下がるなど、機械で設定した通りには温度管理できないことがほとんどです。
設定温度を超えてしまう現象を、私が勤めていた工場では「オーバーシュート」と読んでいました。
オーバーシュートが起きる条件
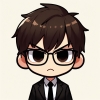
オーバーシュートが起きる条件に、違いはあるの?
例えば、化粧品を作る装置で原料を加熱し混合しているとします。
装置に、
- 10kgの原料が入っている
- 100kgの原料が入っている
この2つでは、温度の上がり方が全然違います。
加熱により装置全体が温まります、容量が少なければ少ないほどに、設定温度に到着した後も温まった装置の熱を吸収していきます。
ですから、①と②の場合、①の方がオーバーシュートの現象が強く、設定温度より大きく上昇してしまうのです。
到達したい設定の温度は「目標の温度より低く」設定することが基本となります(冷却の場合は逆になります)。
そして、装置の容量に対して化粧品を作る量が少なければ少ないほどに、オーバーシュートの現象は強いと考えましょう。
気を付けないと、装置の中がグツグツと煮えたぎってしまうこともあります。
オーバーシュートで発生するミス
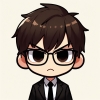
ちなみに設定温度より高くなってしまうと、どのような問題があるの。
「油」はオーバーシュートが起きやすい傾向にあります。
化粧品原料とは天然由来も多くあります。特に植物系の油などは多くの種類があります。
これらの原料を加熱するのに温度を上げすぎたり、温度が高い状態が続いたりすると、「匂い」が強くなります。
最近は無香料の商品も多くなりました。香りがついてないものは特に、使用する原料の油が、いつもよりも「油臭い」では、製品として「不合格」となります。
そして、設定温度を超えるオーバーシュートの問題は加熱だけではありません。
加熱後に冷却し、目標温度を40℃にて「香料」を添加するとします。
40℃に設定したのに35℃まで下がってしまうと、クリームであれば、冷えて固くなることもあります。
40℃であれば、まだ柔らかい状態であったので「香料」も簡単に混ざったのですが、35℃で固くなってしまうと、中々混ざってくれません。
混ぜるために、いつもより時間をかける必要があります。
しかし、いつもより時間をかけることは危険な行為です。混合時間が長すぎたことで、本来の固さより柔らかく出来てしまうことがあるからです。
たかが5℃や10℃の温度をミスっただけで、せっかく作った化粧品が不合格になることはあるのです。
どうすればいい、オーバーシュートの対策
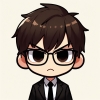
何を注意すればいいんだろう?
次のことを意識しましょう。
- 化粧品を作る量の違いから「オーバーシュート」の現象にも差が出る。
- 使用する原料の違いから「オーバーシュート」の現象にも差が出る。
「オーバーシュートの現象」はいつも同じ条件ではないことを、まずは認識しましょう。
経験が浅ければ浅いほどに、目標温度の設定は低くして、目標温度の手前からは調整しながらにしましょう。
そして、これらの条件以外にも、使用している装置のメーカーによって、オーバーシュートの現象にも差があります。
国内の有名メーカーであれば、オーバーシュートを自動で抑える装置が付いています。設定温度手前で、スイッチのON、OFFを繰り返すことで、目標に近い温度にたどり着きます。
しかし、原料の種類などを識別するわけではないので、間違いなくオーバーシュートは起きます。
そして、自動の機能もメーカーによって差があります。もしかすると、オーバーシュートを自動で抑える機能がないこともあるかもしれません。
私が経験した工場では、数社の違うメーカーの装置が並ぶ工場もありました。
A社の装置を使った後に、B社の装置を使用することがあれば、装置によってオーバーシュートの仕方も違うので気を付けましょう。
発生ミス、その5 バルク製造で起きる「入れ忘れ」
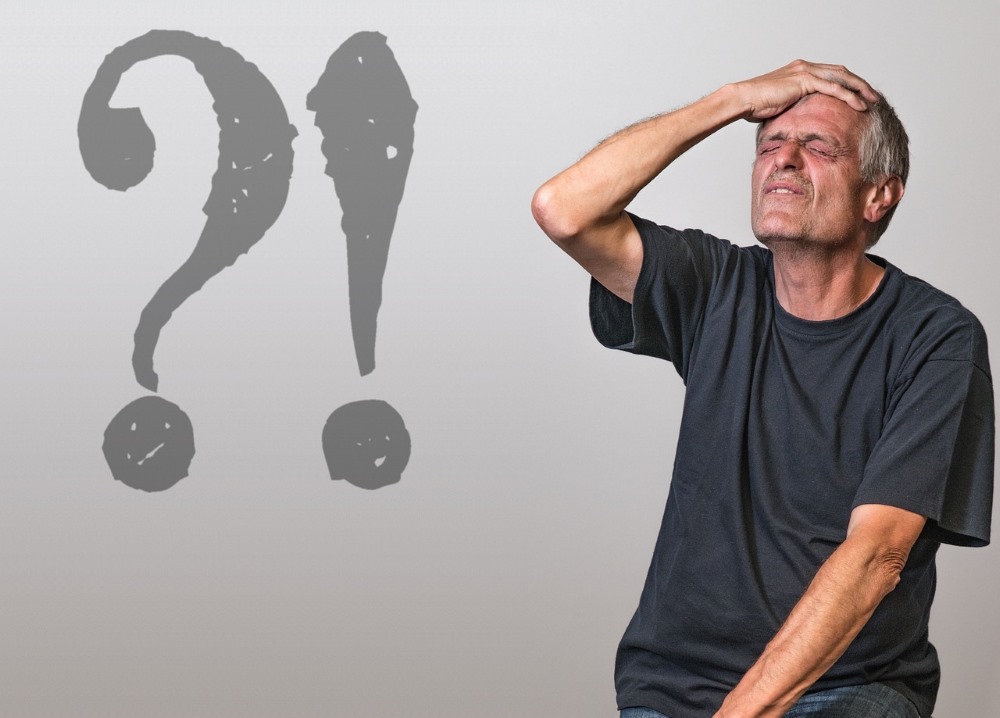
工場にもよりますが、凄く単純でダメージの大きいミスとして「入れ忘れ」があります。
「秤量」という事前に原料を計りこむ作業を終え、その原料を装置に入れて化粧品は作られます。
「入れ忘れ」とは、何かしらの原料を装置に「入れ忘れ」て工程を終えてしまうことです。
当然、その状態は「不合格」であり、再生可能であれば「手直し」となります。
設備の揃っている大手企業であれば、バーコード管理でそのようなミスもほぼゼロかと思います。
私がいる工場では、そのような設備はないので、稀に起こる「ミス」です。
入れ忘れが発生するのはなぜ
原料を装置に入れるのは本来ダブルチェックが基本です。
装置を扱って化粧品を作る担当者が、秤量済みの原料を持ち出します。
まずここでチェックです。
そして、装置へ投入するのですが、ここのチェックを、化粧品を作る担当以外の人がします。
この2つで、ダブルチェックとなります。
チェックが徹底されていれば、まず「ミス」は起きません。ですから「ミス」の原因はチェックがしっかり実施されていないことです。
忙しい状況で人が動き回っていたりすると、チェックを依頼することを遠慮してしまうことがあります。
とくに新人は、忙しい人に声をかけることをためらいます。
「忙しそうだし、自分でチェックすればいい」そのように思ってしまうと、次も、その次も、1人でチェックしてしまいます。
本来のダブルチェックではないので、既に逸脱行為です。
そして自分もバタバタと忙しくなると、チェックが抜けて「入れ忘れ」るわけです。
原料を入れ忘れしたら、どうなるのか
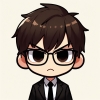
入れ忘れたなら、後から入れたらダメなの?
「手直し」として、添加出来るものとできないものがあります。
単純に工程の最後の方に添加するなら、工程が終わってからでも添加が出来ることがほとんどです。
しかし、冷却する前の加熱の工程で添加する原料であれば、手直しできない事がほとんどです。
加熱している時に添加する原料は、同然ながら高温で添加する必要があります。
工程をすべて終えてから「入れ忘れ」に気付いても、既に冷却後の冷えた状態です。それを再度、加熱して手直しすることは基本的に出来ません。
冷却してから添加する原料はいくつかあります。なぜ、冷却してから添加するのか、「熱に弱い」からです。
熱に弱い原料を入れてから、入れ忘れがあるとはいえ、再度、加熱することは出来ないのです。
「入れ忘れ」とは「不合格」以前に、「入れ忘れ」により、工程が終了しない廃棄物となる最悪な「ミス」なのです。
どうすればいい、入れ忘れの対策
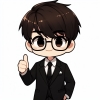
チェックを徹底するしかないわけだね。
そういうことです。
しかし、それで済ませても「ミス」は減りません。
なぜチェックが抜けてしまうのか、
- 作業の負荷
- 秤量した原料の置き場
- ダブルチェックを依頼しにくいコミュニケーションの不備
このようなことまで考えましょう。
もちろん新人が考えることではないですが、一番、新人がミスを犯すリスクがあるのですから、勇気をもって上長に相談しましょう。
どうしても忙しいと、ルール化したものが崩れていきます。
そのルールによって一番守られているのは経験の浅い新人なのです。本来のルールと、何が実行しにくいのか、話し合う必要はあります。
ミスを防ぐために必要な行動と意識
特に新人が陥りやすい「ミス」を5つご紹介しました。これは、私が見てきたり実際に体験した内容になります。
誰でもミスは起こします。しかし、連続して発生するミスほど、部内に重い空気を発生させるものもありません。 日ごろから意識し、行動できることは実践しておきましょう。
そこから徐々に身につけたものがスキルとなり、ミスをなくしていくわけです。
認識違いによるリスクをなくす
担当する製品は事前に上長とミーティングしておくことが理想です。実際の工程をシミュレーションすると、認識違いなどが見つかることも多いです。
コミュニケーションを取る
化粧品を作るバルク製造部門は「チーム」と考えましょう。個人の担当や責任はありますが、あくまでもチームとして仕事をしていることを忘れないようにしましょう。コミュニケーションを取ることで、情報の共有や認識の違いなども減ります。
作業環境の整備
仕事をやり易くするための工夫や、作業の効率化、ミス防止のための環境づくりや整理整頓は重要です。
スキルを高める
何を意識して仕事をするのかを理解し、仕事をしながら何を学ぶべきかを考えることが重要です。また、具体的な目標を持つことも忘れないようにしましょう。ただし、自分自身への負担にはならないようにし、上長を上手く活用することも考えましょう。
改めてルールの確認
ダブルチェックのように幾つかのルールは存在しています。あらためて、どのようなルールがあるのか確認しましょう。知らなかったり、忘れていることがあれば、その必要性を確認してから実施しましょう。
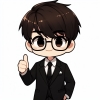
特に同じ「ミス」が何度も発生するようなら、間違いなくルール化されたものがあります。自分を守るためにも、問題があれば「確認」しましょう。
ミスが起きれば発生原因を特定し、それに対する対策と実施する計画が必要です。
しかし、新人などの経験が浅い立場であれば、声を上げるのも難しいでしょう。
だからこそ、コミュニケーションを取りながら、自分が「ミス」を発生させないために、出来ることを見つけるということです。
ここまで読んでいただいた方はそれを見つけたかと思います。
これから、もしくは、これからも、化粧品を作る仕事に携わる方には、「ミス」を回避する能力が、多少なりとも身に付いたのではないでしょうか。
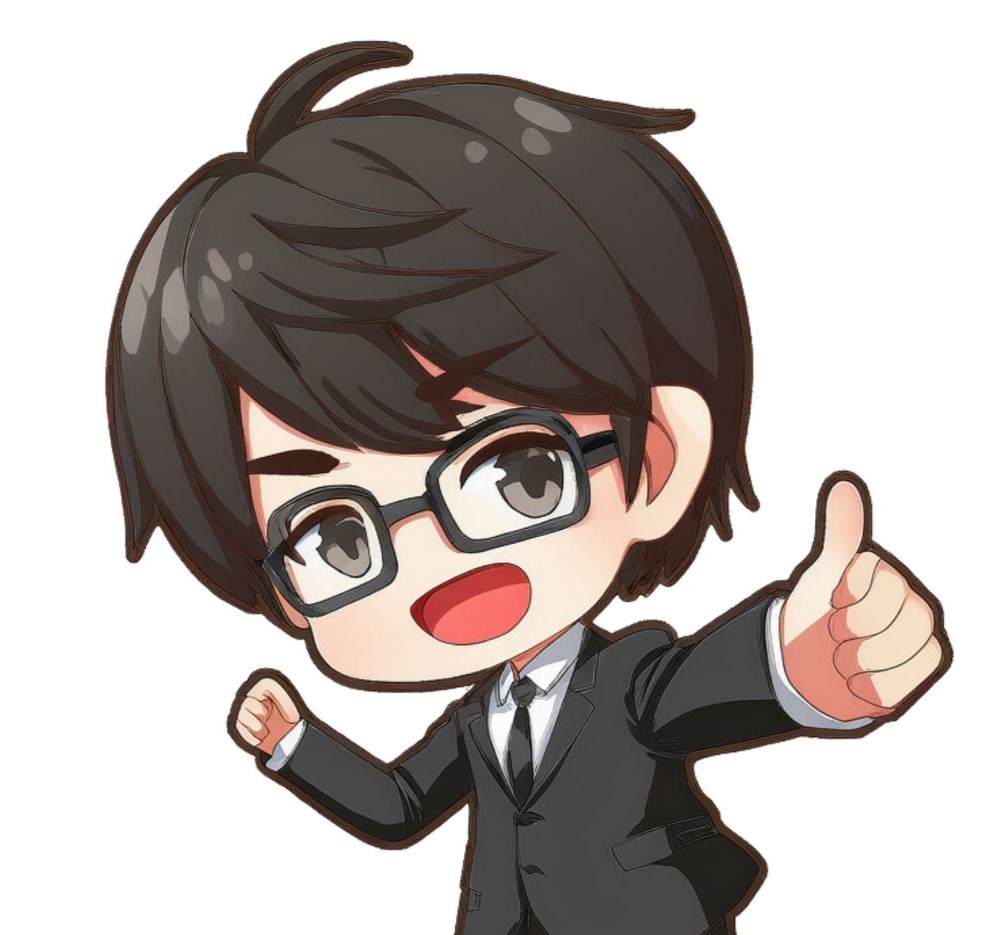
バルク製造の技術を身につけるほどに、どこの化粧品工場でも活躍できる可能性が高くなります。
化粧品の「匠」を目指して頑張ってください。
もしもこの記事を読んで、化粧品を作る仕事が合わないと感じたとしても、化粧品工場で働くことをあきらめないでください。化粧品を作る以外の他の役割も探してみてください。
化粧品工場の仕事内容は様々です。どのような仕事が自分に合うのか、以下の記事をご参照ください⇩
化粧品工場で働くための転職活動
化粧品工場の仕事に興味があり転職を考えているなら、情報収集から始めましょう。
当サイトは化粧品工場に関する基礎知識や、私が勤務した工場での事例を多く提供しています。自分がチャレンジすべき仕事であるのか、多くの情報から確認しましょう。
そして、転職する決意と、やりたい仕事が明確であるのなら、おススメするのは転職サービスです。
私も経験がありますが、転職してから「この仕事ダメだ!」思うこともあります。
その度に転職を繰り返しては、履歴書の職歴を増やすだけで、あまり良いこともないでしょう。とはいえ、求人サイトの情報だけで、自分にピッタリの仕事を見つけるのも困難なものです。
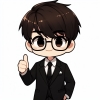
転職のために、何社も面接を受けるのは大変ですよね。
転職を考えるのなら1人ではなく、転職のプロであるキャリアコンサルタントを味方につけましょう。
- 同業界出身担当によるサポート
- 内定者満足度99.2%
- 異業種転職にも活用
- 転職支援実績も豊富で安心
フミダスでは、あなたと同じ業界出身のキャリアコンサルタントが、転職活動を全面的にサポートします。
同じ業界出身だから、あなたの経験に理解があり相談しやすい!そして、同じ目線で考え、あなたが求める転職をサポートできる。
あなたの担当が、同じ仕事の経験をもつキャリアコンサルトであることが、この転職サポートの強みです。
今のまま、ずっとこの職場で働くのがムリだと感じているのなら、まさに一歩踏み出すために、相談してみましょう。
あなたが求めるものをすべてアドバイザーに相談!
化粧品工場で新たな可能性をつかむ!
化粧品工場での業務は、想像しているよりも手に入れやすいです。
資生堂やコーセーのような大手化粧品メーカーは一定の学歴や経験を求めることはありますが、日本全土には中小規模の受託メーカーを含めて、数千に上る化粧品工場が存在します。
多くの工場では、幅広い職種で正社員としての雇用の機会があります。
化粧品工場で働くことに興味があるなら、そこは新たな可能性を提供する場となるでしょう。
勇気を持って一歩を踏み出し、その機会をつかむことをお勧めします。
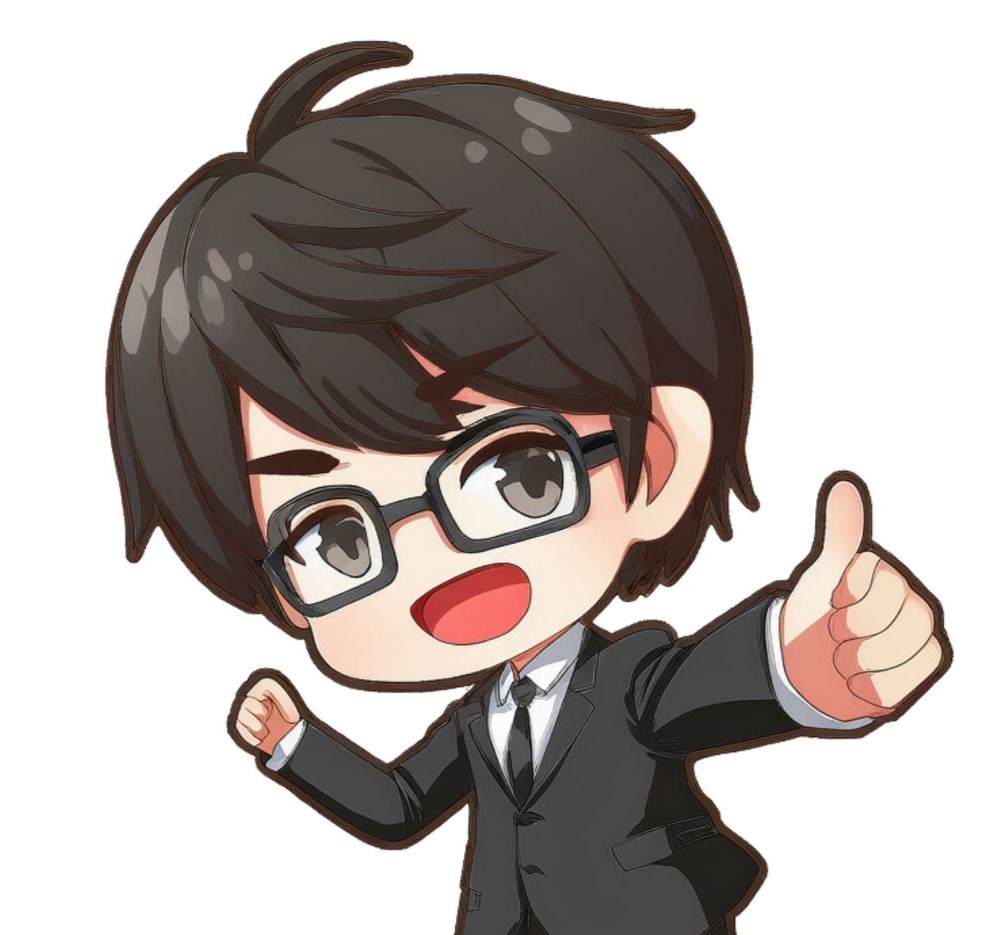
応援しています。
化粧品工場の仕事で最初に「きつい」と感じることって何でしょう?あなたにとって苦手なことがないか、確認しましょう⇩
ライン作業を管理する「充填・包装」の仕事を説明しています。興味のある方はご参照ください⇩
最後までお付き合いいただき、ありがとうございました。
良い職場との出会いを祈っております。